Quality is an important aspect of sustainability – “A durable product is the cheapest to use”
150,000 test cycles. That’s the number of times a piece of wood formed into the shape of a bottom is thrust into the seat of Martela’s universal chair in our testing laboratory before it finally enters the market. In the case of a universal chair designed for non-domestic use, for example in the visitor and public areas of an office building, the backrest, armrest and front edge of the chair are also subjected to almost a quarter of a million of test cycles. A chair used in a public space is always in heavy use, so it is subjected to the most loading, rolling and bending.
An office chair is subjected to even more tests on its various functions, such as the castors and the adjustable gas spring.
A piece of furniture is tested at the concept stage, the prototype stage and throughout its journey to finished product model. This means that when a finished product reaches the type approval stage there are rarely any surprises.
In addition to the European EN testing standards, Martela has its own criteria. When a decision is made to launch a product, it is not enough to fulfil product standards alone, as the product must also feel right, be visually appealing and the design language must also stand the test of time.
There are separate standards for the different categories of furniture used in public spaces, such as task chairs, desks, storage units, school chairs and school desks. The flexibility of shelves and the durability of their various components are tested. Tables are subjected to loading from various sides and a task chair’s gas spring is put under strain and the castors are subjected to heavy use. A task chair can have 7–8 different moving parts, so testing this type of chair takes the most time. “Testing typically takes 6–8 weeks, day and night, which is equivalent to 10 years of use. We simulate a situation of normal use and a little bit extra,” says Jarno Forsman, Laboratory Engineer at Martela.
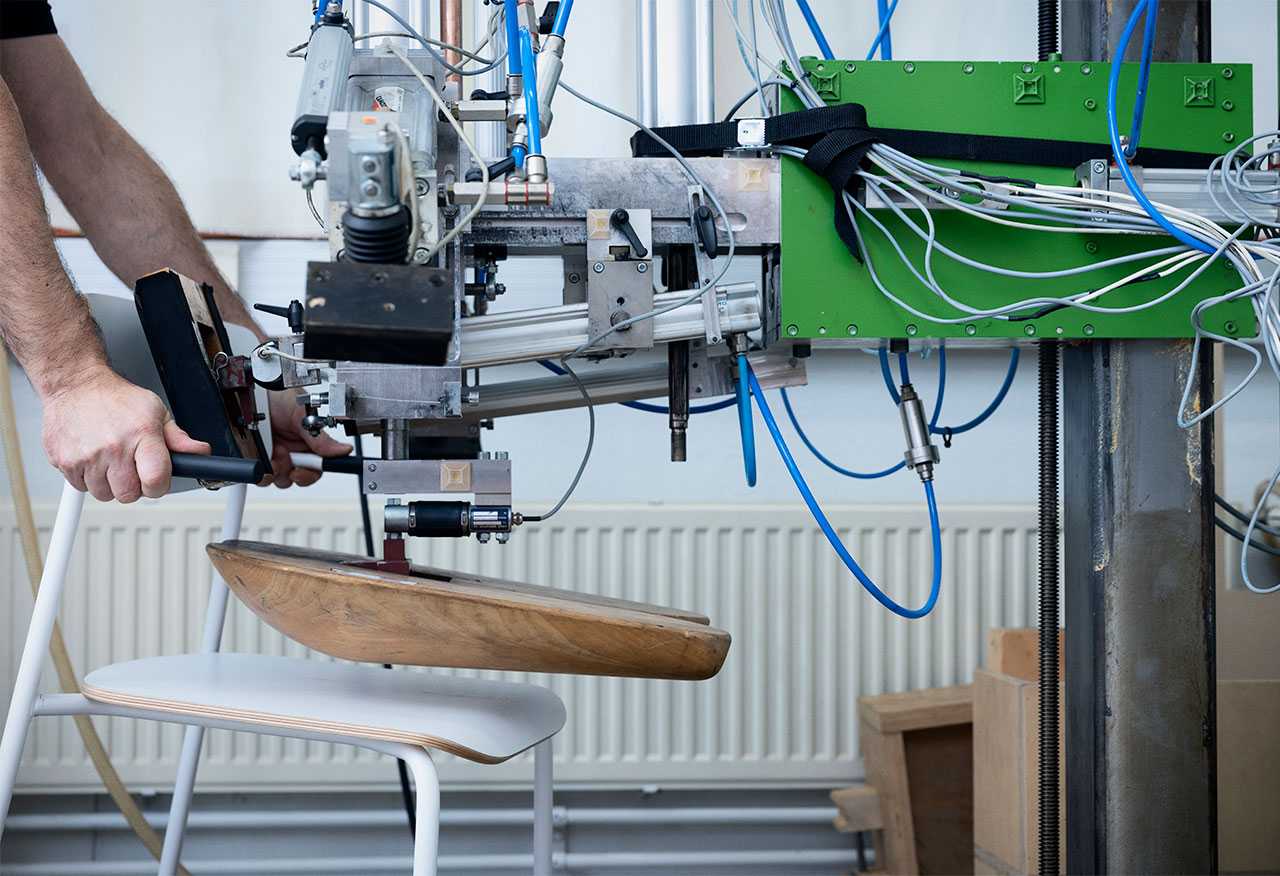

Finland’s only testing laboratory dedicated to testing of non-domestic furniture
The testing laboratory in Nummela is unique, as it is the only laboratory in Finland that is accredited to carry out testing according to 20 non-domestic furniture standards. The accreditation that has been granted by a third party means that the test results obtained in the laboratory are reproducible and comparable with those of other accredited laboratories.
The Nummela testing laboratory was established in 1991, and since then Martela’s representative has been actively involved in the development of European testing standards for furniture intended for non-domestic use. Martela’s testing laboratory received its first accreditation in 2013 and its current accreditation was granted at the end of 2021. The nearest testing laboratory accredited for the corresponding product standards is in Sweden.
Quality equals sustainability
Standards for office furniture are not yet mandatory, unlike standards for children’s high chairs, for example. At Martela, testing is, however, above all about quality and consequently sustainability.
The EU already requires the life-cycle costs of products to be taken into consideration in public procurement.
A high-quality product has a longer life cycle than a product that has been poorly manufactured. High-quality products also have more potential to be recycled and reused than products that have been manufactured based on the latest trends or low prices.
“Price competition is fierce, and it’s easy to compare prices. Consumers and organisations do not, however, have access to similar tools for comparing the quality of products that are equally easy and cheap to use. Testing carried out by an accredited laboratory is the only comparable way to ensure that a product will really stand up to use,” says Anne-Maria Peitsalo, Director, Sustainability & Quality at Martela.
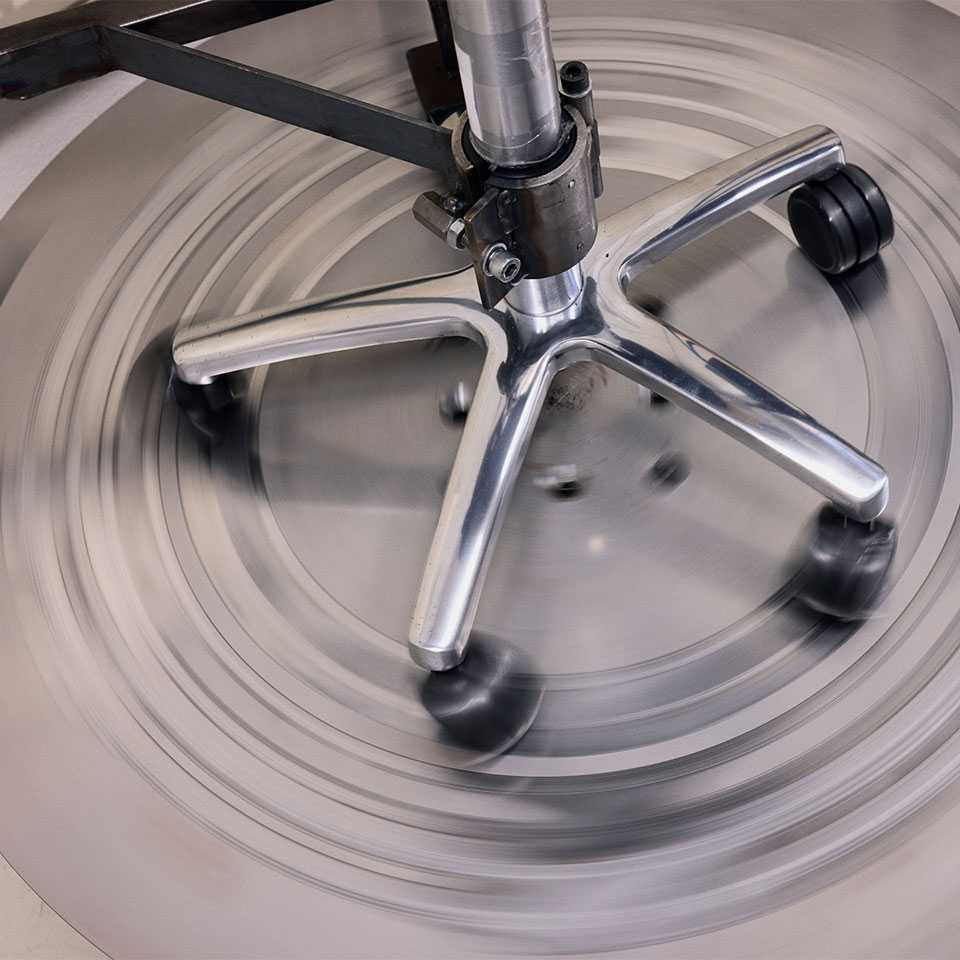
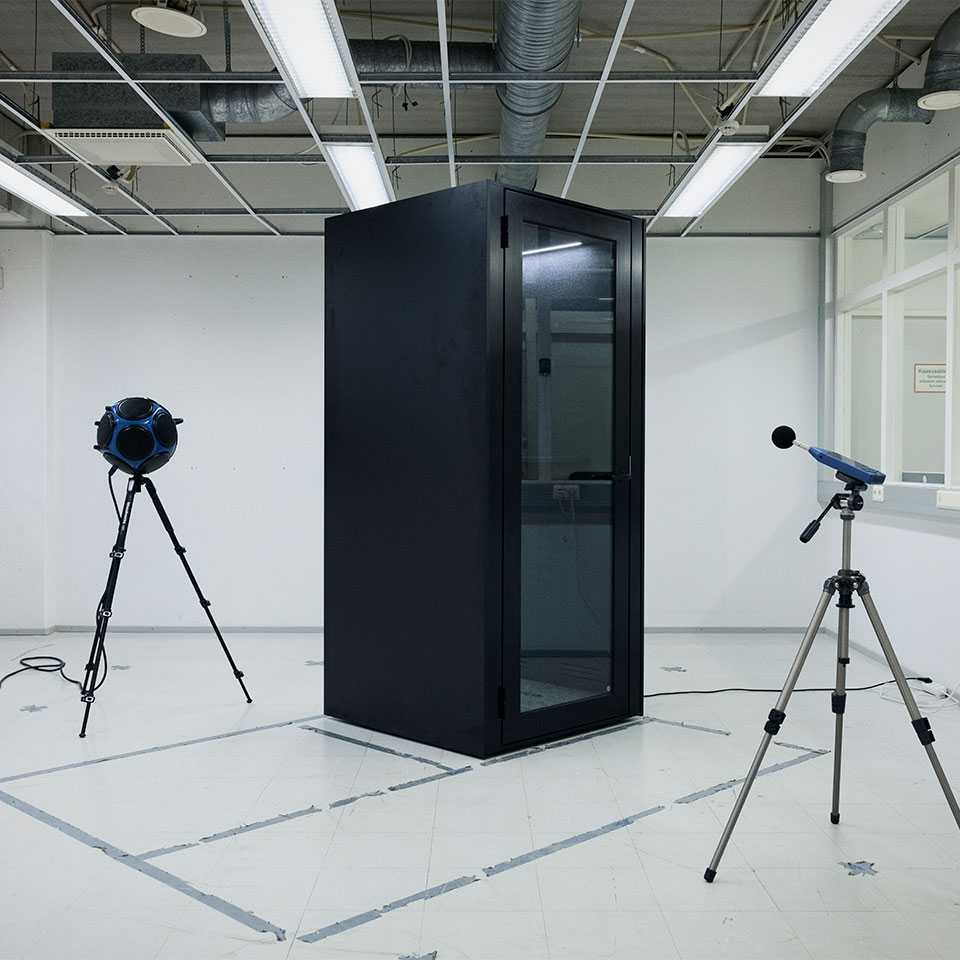
High-quality products from the outset
The testing laboratory is also a selling point. Visitors to Nummela have the chance to see what is being tested and how testing is done in practice.
“We don’t need to provide visitors with any more justification for why quality is important. It's nice to see the visitors gaining a sense of realisation and to see their understanding grow,” says Forsman.
Martela emphasises the connection between quality and sustainability. There are also practical benefits.
“For us, the most affordable product is a durable product,” says Forsman. “Maintaining a high level of quality pays itself back in the long run. A high-quality product gets fewer complaints. It is always more difficult and expensive to repair something than it is to produce a high-quality product in the first place. Testing is also a form of optimisation. It means we do not use too much material in the products we introduce to the market, which is not only more environmentally friendly but also cheaper,” he says.
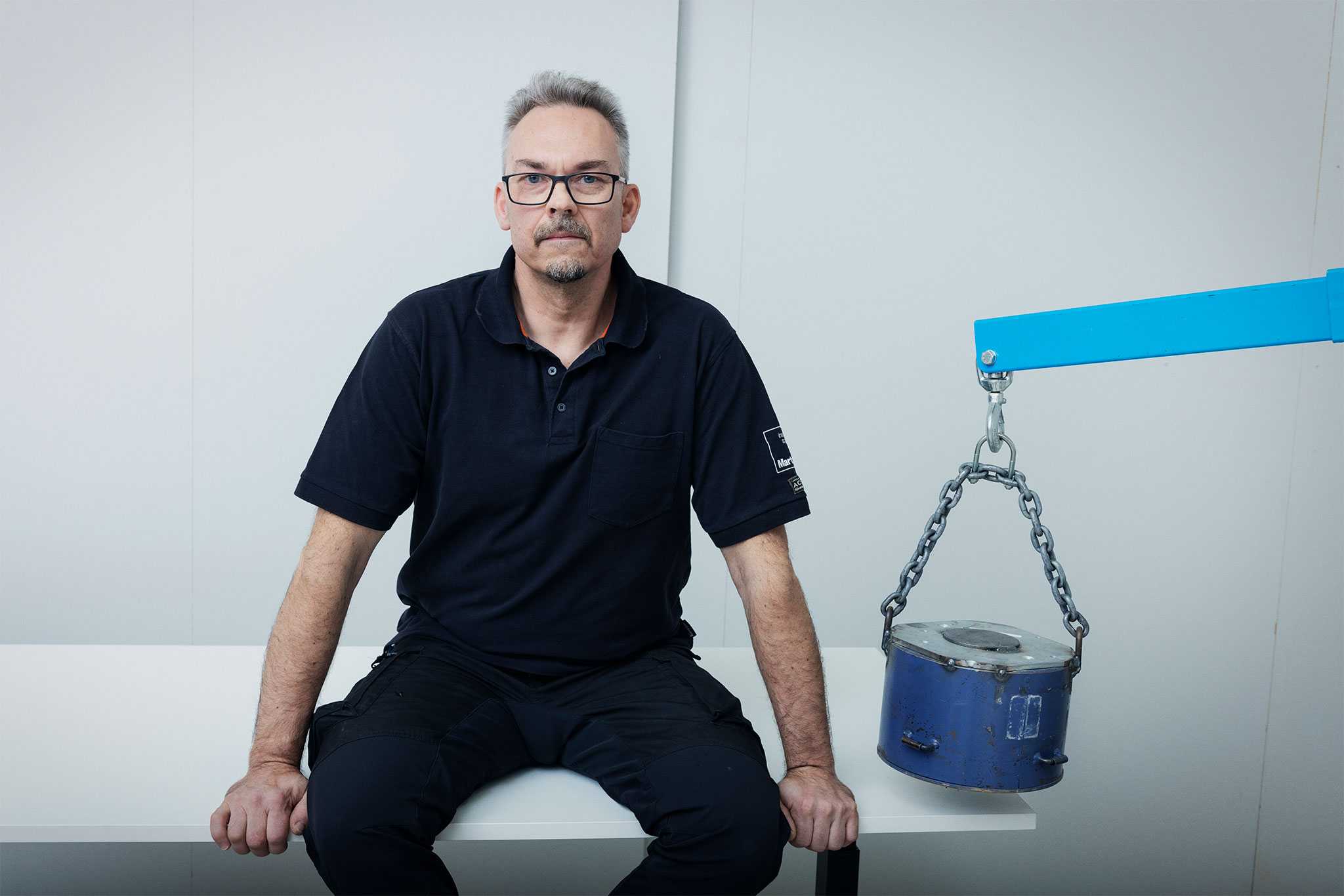
Read more about sustainability at Martela!
Read more about Martela’s quality standards!
Read more about accreditation on the FINAS website.